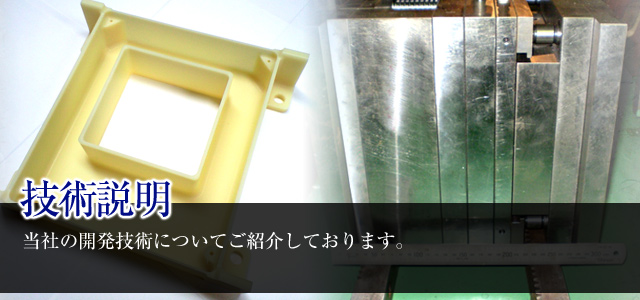
もともと英語で「柔軟に形を変えられる」という意味をもつプラスチック(plastic)は、強く、軽く、腐らず、衛生的で加工しやすく、大量生産も可能なことから、私たちの身の回りで多く使われております。
また、熱を加えると簡単に形を変えられるため、リサイクルが容易で環境負荷の低減するという観点から今後もそのニーズは増えていくとされております。代表的には、食品容器や袋をはじめ、自動車部品、スマホ、携帯ゲーム、など限りありません。
光産業ではそれらプラスチック製品を設計開発から成形・加工と一貫して行っており、ここではそのうちの代表的なプラスチックをご紹介いたします。
![]() |
![]() |
|
![]() |
![]() |
JIS規格では、「高分子物質を主原料として人工的に有用な形状に形作られた固体である。ただし、繊維・ゴム・塗料・接着剤などは除外される。(JIS K 6900)」と定義されています。
※タイトルをクリックで開閉します。
まず、プラスチックの主原料の原油を、蒸留しナフサを取り出します。さらにそれを分留してエチレンやプロピレンなどの合成樹脂や石油化学製品の基礎原料を取り出します。
そして、それをまた他分子と結合・重合などすることで多様なプラスチックを生産します。と、何段階もの工程を経て、プラスチック材料が作られています。
また、現在では、石油以外(穀物でん粉など)を原料にしたプラスチックも量産されています。
プラスチックは【熱可塑性樹脂】と【熱硬化性樹脂】に大別されます。光産業では熱可塑性樹脂の成形加工を得意としています。この熱可塑性樹脂はチョコレートの様に溶かせば何度でも形を変えることができます。
熱硬化性樹脂は、クッキーのように熱を加えると硬化し、再度溶融して使用することができない性質を持っています。熱に強く灰皿などに使用されています。
※可塑とは固体に熱などの外力を加えて変形させ、力を取り去ってももとに戻らない性質のこと
下記に、加工可能なプラスチックの紹介と簡単な解説を掲載しました。
熱可塑性樹脂 | 樹脂名 | 耐熱温度(℃) | 用途 |
---|---|---|---|
高密度ポリエチレン HDPE |
90〜110 | 理化学容器・キャップ | |
低密度ポリエチレン LDPE |
70〜90 | プラスチック容器用中栓 | |
ポリプロピレン PP |
100〜140 | 生活雑貨・弁当箱・哺乳瓶 | |
ポリスチレン PS |
70〜90 | 透明ケース(廉価) | |
AS樹脂 AS |
80〜100 | 透明容器(要強度) | |
ABS樹脂 ABS |
70〜100 | 電気製品・民生用電気製品(弱電分野) | |
ポリアセタール POM |
80〜110 | 機構部品・ダーツの針 | |
ポリブチレンテレフタレートPBT | 210 | 電子部品・工業用電気機器(重電分野) | |
アクリル PMMA |
70〜90 | キーホルダー・はんこの握り | |
ポリカーボネート PC |
120〜130 | 波板・建築部材 | |
ナイロン PA |
80〜180 | 結束バンド・機構部品 |
この他にも、FRP(繊維強化プラスチック)といって、ガラスやカーボンなどの繊維をプラスチックに混入したグレードも存在します。
安価・軽量で耐久性がよいことから、小型船舶の船体や、自動車・鉄道車両の内外装、ユニットバスや浄化槽などの住宅設備機器に多く使用されています。
光産業では、ガラスによる繊維強化プラスチック(GFRP)の成形も行っております。(≦GF15%)
プラスチック成形をする場合には数多くの留意点があり、これらを網羅的に把握した上で設計をする必要があります。ここでは、その留意点を設計プロセスごとにご紹介いたします。
※項目をクリックで開閉します。
まずは、作りたい製品のスケッチや構想を練ります。(こんな物が有ったら便利だなぁ。など)
この段階では、金型からの離型方法や材料コストなどは検討しません。制約なしに自由な発想の中でアイディアを出します。
製品の図面を作成します。基本的にはCADを用いて設計していきます。
その際の一番の注意点は勘合部です。たとえば、Φ10の穴にΦ10の棒は入りません。
Φ10の穴に棒を差し込む際は、棒をΦ9.8〜Φ9.9等のように少し小さく設計します。
また、金型から離型しない構造では製品は作れないので、離型方法も考慮しながら設計します。
抜き方向を考慮しないと、スライド機構が余計に必要になってしまったり、冷却機構が難しくなったりするため、金型コスト増や成形品の寸法不適合や外観不良を招きます。
プラスチックには多くの種類が存在しますが、それぞれコスト優位性・耐衝撃性・耐薬品性・耐熱性・難燃性・透明性・耐候性など多くの優れた特徴を持っています。
しかし、すべての特徴を兼ね備えたプラスチックは存在しないため、製品のコンセプトにあった機能の取捨選択をしなくてはなりません。
以上のように、材料の特性を考慮しながら製品を考えなければなりません。
そして、ここまでが製品の設計となります。
ここからは、実際に製作という工程になっていきます。金型を製作する際も留意点があります。
製品を寸法・外観ともに効率よく安定して作らなければなりません。
そのためには、プラスチックの収縮率・成形品の抜け勾配・パーティング面・冷却構造・ゲート位置及び構造・取数などさまざまな検討をしなければなりません。
製品単価を安くしようとする場合は、ピンゲートといわれる構造でなおかつ多数個取を検討します。
しかし、肉厚のアクリルなどは流動性が悪く高圧で成形する必要があるため多数個取もできません。また、取数は金型のコストと比例するため、製品ごとに最適な妥結点を検討します。
良好な金型を製作できたらいよいよ成形です。
成形もコストを考えると、ハイサイクルが理想ですが必ずしもハイサイクル成形ができるとは限りません。
流動性の良いプラスチックは充填スピードを早くすると同時に、金型温度を低く維持し冷却時間を短くすることができますが、アクリルやポリカーボネートなど流動性の悪いプラスチックは流動性を良くするために金型の温度を高くしてゆっくりと充填しなければなりません。
それと同時に、金型温度が高いために冷却・固化にかかる時間も増えます。そのため、ハイサイクル成形はできません。
また、プラスチックには親油性プラスチック・親水性プラスチックがありポリエチレンなどのオレフィン系樹脂は乾燥を必要としませんが、ナイロンに代表される水を含みやすい樹脂は予備乾燥が必要になります。
乾燥温度・乾燥時間もプラスチックの種類によって異なり、場合によっては設備も変更しなければなりません。
これらは検討事項の一部に過ぎません。光産業では、開発から成形までを一貫して支援・提供いたします。ぜひ一度、ご相談ください。
プラスチック成形では、それぞれの材料の特性を十分理解した熟練作業員が、不良の原因とそれに合った対策を講じなければ良好な成形品を作れません。弊社では射出成形に関して、マニュアルを作成し成形品の不良と対策を行っております。
作業員のレベルに関わらず誰でも良好な製品を作れるように日々改善を行っております。
無論のこと、成形品の不良対策を施した場合には熟練作業員が最終確認を致します。
以下に、代表的な成形上の不良とその対策方法を紹介いたします。
※タイトルをクリックで開閉します。
![]() |
||
|
||
![]() |
||
|
||
![]() |
||
|
![]() |
||
|
||
![]() |
||
|
||
![]() |
||
|
![]() |
||
|
||
![]() |
||
|
||
![]() |
||
|
![]() |
||
|
||
![]() |
||
|
||
![]() |
||
|
![]() |
||
|
||
![]() |
||
|
![]() |
||
|
||
![]() |
||
|
![]() |
||
|
||
![]() |
||
|
||
![]() |
||
|
![]() |
||
|
||
![]() |
||
|
||
![]() |
||
|
![]() |
||
|
||
![]() |
||
|
||
![]() |
||
|
![]() |
||
|
||
![]() |
||
|
||
![]() |
||
|
![]() |
||
|
||
![]() |
||
|
||
![]() |
||
|
![]() |
||
|
||
![]() |
||
|
||
![]() |
||
|
![]() |
||
|
||
![]() |
||
|
||
![]() |
||
|
![]() |
||
|
||
![]() |
||
|
||
![]() |
||
|